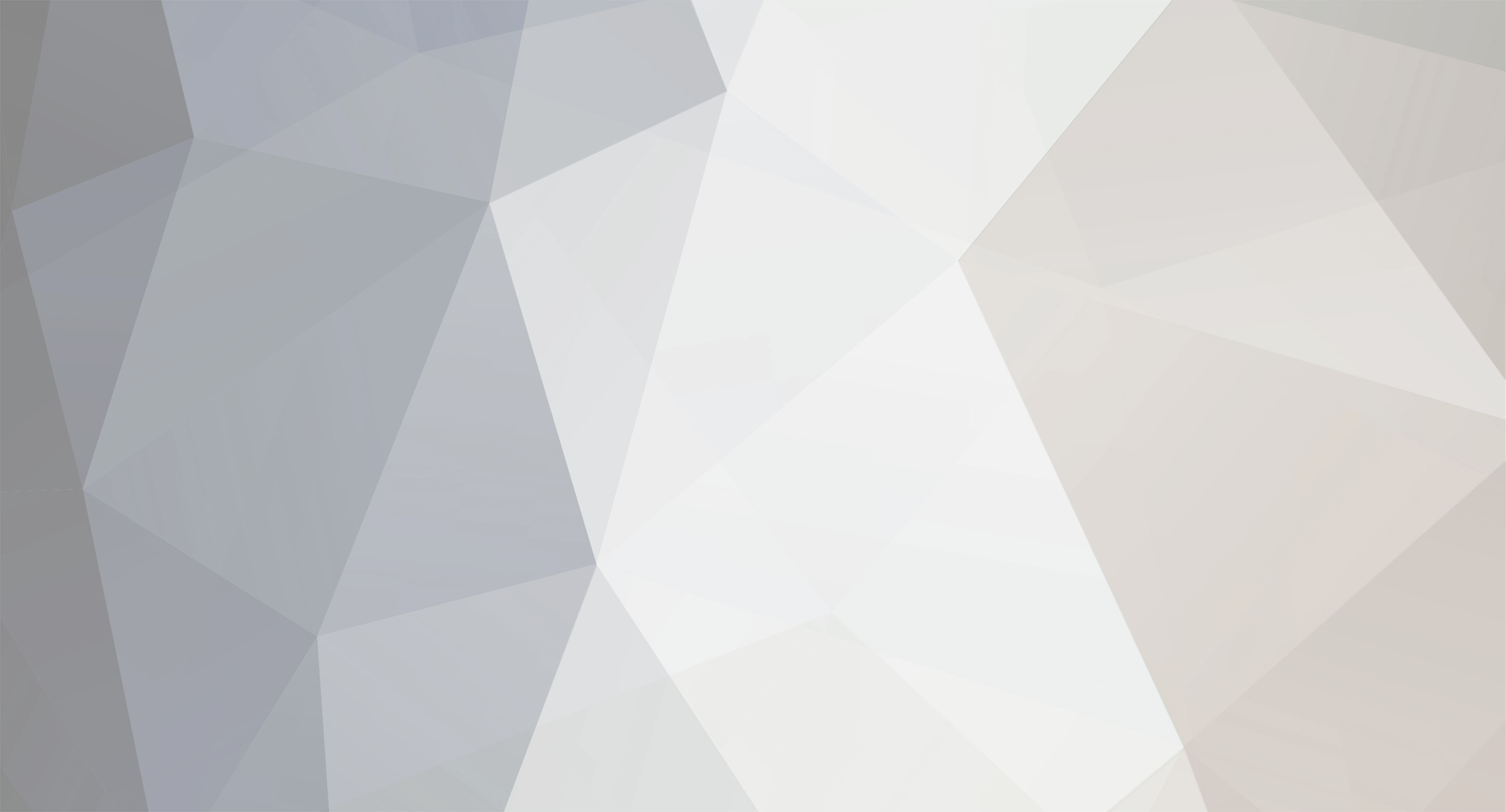
wollyjumperuk
Registered users-
Posts
85 -
Joined
-
Last visited
Content Type
Profiles
Forums
Events
Store
Gallery
Community Map
Everything posted by wollyjumperuk
-
BMW K75RT Ultima FOR SALE
wollyjumperuk replied to wollyjumperuk's topic in For Sale and Wanted - Motorbike related
Afternoon all, thank you for your interest - this is now sold! -
BMW K75RT Ultima Restoration
wollyjumperuk replied to wollyjumperuk's topic in Old Motorbikes, Projects and Restorations
If you are interested in her, please find the full advert on the for sale section of the forum and the auction on eBay via https://www.ebay.co.uk/itm/254655643986 -
BMW K75RT Ultima FOR SALE
wollyjumperuk replied to wollyjumperuk's topic in For Sale and Wanted - Motorbike related
Just realised I'd not popped the ebay link on here! She is for sale via https://www.ebay.co.uk/itm/254655643986 -
BMW K75RT Ultima FOR SALE
wollyjumperuk replied to wollyjumperuk's topic in For Sale and Wanted - Motorbike related
Would it make life easier if I said offers in the region of £3,000? -
BMW K75RT Ultima FOR SALE
wollyjumperuk replied to wollyjumperuk's topic in For Sale and Wanted - Motorbike related
You could look at one now! -
Welcome to the advert for my K75 (https://www.ebay.co.uk/itm/254655643986)with 37507 miles on her, I've just sat down to write this on returning from the MOT station where she passed with no advisories! The bike was sold to me a few years ago and during my ownership I have stripped back, extensively refurbished and rebuilt the bike, the details of this can be found on my blog: https://motorcycleprojects.wordpress.com/ To give you an idea of the work undertaken, the highlights are: Fixed and completely repainted bodywork, frame and components Progressive fork springs and fork service Headstock bearing replacement Mirror tethers (to stop you losing them if they get knocked off) Replacement battery 2 new tyres Spline lube service YSS rear shock Installation of clutch pushrod grease nipple Pannier liner bags Stainless steel nuts and bolts Service (bevel box, gearbox and engine oil, filter, etc.) Too many things to list really, using genuine BMW parts wherever possible and bar giving her a clean (which I will do before sale), she is good to go. To accompany all of this is a wad of receipts to evidence all of the work done. I'm really happy how the project has gone and I was planning on keeping the bike, but on going for a ride after the MOT I found the bike was not for me - a great distance or or motorway bike, but due to an impending child I doubt I will be able to go on many more motorcycle holidays with just my wife for company! So, grab yourself a bike that is in as good condition as I could get it with a few years efforts! Viewings are available but are subject to me being free, please contact me for details. Unfortunately these will have to be socially distanced and without test ride unless you can show fully comprehensive insurance to cover this - if you bin it down the road after all that work I doubt if anyone would be OK with that! As mentioned above, we are expecting a child at the moment and we are close to the due date, so please be patient with getting back to you on any questions, arranging viewings and collection. With all the work that has gone into this, I am looking to get around £3,000 for the bike - cash on collection N.B. Buyer to collect or I am happy to deliver the bike to you, but it will be at the cost of a van and fuel (so I can get home again), paid before the bike is delivered at an agreed rate.
-
BMW K75RT Ultima Restoration
wollyjumperuk replied to wollyjumperuk's topic in Old Motorbikes, Projects and Restorations
With the MOT roadworthiness test identifying no issues at all, I was a happy chappy! With that done and the bike good to go she was given a good clean and taken for an extended ride. Although I was happy with the work done, she doesn’t suit how I ride, as you can imagine I was disappointed. So, the final news on the BMW K75RT Ultima is that she will be for sale just as soon as I’ve identified where I want to list her, totted up how much it’s cost (as I’ll list for that price, effectively the buyer will get the labour for free) and written an advert describing as much as I can of the work done. Watch out for the advert! In the meantime I would like to thank people and organisations who have been key in making the restoration/refurbishment possible and otherwise haven't had any thanks so far: Heritage Stickers (http://www.heritagestickers.eu/cat/) - especially for custom printing the paint code stickers for me, alongside all the others provided to finish the job off perfectly Brad Angove (https://www.youtube.com/user/BradAngove) - for really useful advice on spray/rattle can painting which really improved the finish I achieved over the last project Chris Harris (https://www.youtube.com/user/BavarianBomberWrench/videos) - for great step by step advice on how to pull various bits of the K75 apart and repair them! Particularly useful for making up studs to realign the gearbox when refitting, spline lubing and removing mirror glass without breaking it (still glad I got that perfect first time)! Shel Smith (https://www.youtube.com/channel/UC78zPlzaTZI2WxAckclwIzQ) - for another source of great step-by step advice (with text explaining bits too!), particularly useful for gearbox and clutch adjustment and boot issues Online forums, such as themotorbikeforum and motobrick for advice in general Motorworks (https://www.motorworks.co.uk/vlive/Home/index.php) - for really accessible new and used genuine BMW parts, I try to avoid using pattern so these guys were really useful eBay and especially Kays Fastners selling via eBay - for all my stainless steel bolt needs! Halfords - for ease of access to paint, colour matched stuff there is great and is only down the road Last but by no means least - my long suffering, ever supportive wife! -
BMW K75RT Ultima Restoration
wollyjumperuk replied to wollyjumperuk's topic in Old Motorbikes, Projects and Restorations
That's the thing, they weren't 'squeaky' but 'creaky', like a door being slowly closed with rust hinges - it was odd. Swapping the pads seems to have done the trick though! To take the switch apart was a bit of an ordeal, but one I got the knack of it, it was OK. The way I did it was: > Put small cross/pozi screwdriver in vice point up > With a flat blade screwdriver ease the rocker part of the switch off > Put the switch body, rocker mounting side down, on the screwdriver in the vice, making sure the screwdriver goes through the same hole the lever of the switch would and sits against the black plastic backing on the far side of the slider > Use a pointy ended dentist tool or very small flat head screwdriver to get in to the back of the switch above each of the tabs and ease these > Apply gentle downward pressure on the switch body and work your way round the 4 tabs, a little at a time, easing the black section out - it might take a bit of time but best to take time and avoid damage It is a bit fiddly, your could always do with 2 extra hands, but don't go in too rough on it otherwise it'll break -
BMW K75RT Ultima Restoration
wollyjumperuk replied to wollyjumperuk's topic in Old Motorbikes, Projects and Restorations
With all of the individual components checked, it was time to go through and see if there were any issues following final assembly. First off, the small oil leak from the front of the engine, which was tracked back to the oil pressure sensor... ... to fix this the engine oil had to be drained back out before the sensor was removed and replaced with a new unit, but with me being far too clumsy, the wire fitting was broken off, so this was replaced, the connection remade and the rubber boot refitted, so job done. Next up was a troublesome front brake, it had bled fine but it was creaking when applied. I always start with the worst case and work back from there (sometimes to my benefit, sometimes not so much), so the front wheel had to come off... ... each disc was then removed and inspected in turn, but no warping or other issue, so everything was rebuilt and reassembled, but the creaking persisted. The calipers were next to be visually checked, but before I got too far into it, I can't say why but I decided to swap the 2 pads over in the right side caliper and on testing it, the creak had completely gone! I'll take that! I then wheeled the bike out of the garage to check nothing was fouling the steering, to which both the fuel and temperature gauge smacked the infill panel... ... so the mounts for the gauges and handlebar angle were played with until I had free turning bars and I was able to read the dials... ... but during this process, a wire become detached from the ABS switch, so this was soldered back into place... ... and the switch popped back into place. With that done, that allowed the bike to be run for a while, run it up and down the drive to clear the ABS check and that warning light stopped blinking, and used both brakes to clear that standard warning light too, everything was working lovely! Unfortunately after about 5 minutes of running the battery started hissing and as soon as I realised, the battery boiled over. As quickly as I could, it was bike off, grab the garden hose and hosed down the bike, partly to dilute off the battery acid and partly to cool everything down as I suspected fire was a possibility. Once everything had calmed down a bit, a pair of gloves went on and the battery was removed, thankfully no acid damage. On investigating the set up, and running the bike on a booster pack, there was no overcharging, so that pretty much ruled out the bike being at fault. The battery was topped up and charged but it failed to hold a charge and one cell was getting really warm, potentially indicating a dead or shorted cell. So a new battery was ordered to replace the failed unit, it was fairly elderly, so I'm not too worried. While I was waiting for the new battery, I got on with checking the other systems with the aid of a booster pack to run the electricals. I discovered that the windscreen only worked once after powering up then failed to respond to the switch, so this was popped out and it was clear that the common power supply had suffered during the playing around with the handlebars. So, with some blind disconnecting of connectors the wiring for the switch was taken out. This allowed the wiring to be unsoldered from the switch and both to be tested on the bench. The wiring had no breaks, and the switch was good for the lowering contacts... ... but when switched to the raising contacts there was no continuity. So the switch was disassembled to allow the contacts to be cleaned, and bent slightly back up, not so far as to stop the switch moving, but enough to ensure good contact. From here the switch was reassembled, electrically tested and found to be good, before put back into place on the bike and tested to make sure it was all good. The next item on the list was the OEM tool kit... ... which was in good order, with nothing missing, so it was put straight into the tail fairing. Lastly I ran through the bike to check as many bits as I could ahead of the MOT roadworthiness test here in the UK. It is rather handy the UK Government publish the test parameters online! Thankfully only a few bits to do, such as a red rear reflector... ... and onto adjusting the headlight aim. To do this I rolled the bike back so the bike was 3.8m from the back wall of the garage and measured the height of the centre of the headlight from the ground and marked this on the window frame as a reference. I was then able to adjust the headlight from being far too low, to just about right via the adjustment knob in the back, bottom right hand side of the headlight, while sat on the bike to s better level. Although I can test the brakes work, unfortunately I can't test brake efficiency or emissions before the test without specialist kit, so we'll have to see what comes back from the test on that. Either way, that's the bike as ready for the test as it can be, so it was booked in, just have to wait for the test now! As always, if you'd like further details, please see https://motorcycleprojects.wordpress.com/ -
BMW K75RT Ultima Restoration
wollyjumperuk replied to wollyjumperuk's topic in Old Motorbikes, Projects and Restorations
With the bike done, just need to finish off by completing the luggage, starting with the top box, which was popped onto the bench… … and dismantled, ready for checking over and cleaning up. On inspection I was quite lucky with this one, as nothing needed replacing. Each piece was cleaned up with muc-off motorcycle cleaner, dried off and reassembled… … including the underside foam strips to protect the luggage rack and at this point the catch on the inside of the top box was adjusted to ensure a good fit when closed, rather than the rattle I got from the loose initial fit – I doubt the seal will work with the lid bouncing around as the catch wasn’t holding it tight. I wasn’t happy with the finish of the box once cleaned and reassembled, there were a lot of shallow scratches and a couple of really quite deep gouges. I don’t want to ‘erase’ the history of the bike, but I do want it to have a fairly tidy finish. With that in mind, I gave the areas of lighter scratches a sanding with 1000 grit wet and dry paper, with a few sprays of water to smooth the finish as much as possible. In addition to this I rubbed the top box very sparingly with linseed oil via a lint-free cloth to bring back the original finish, starting on the right (showing the contrast below)… … before finishing off both the remainder of the plastic box and the rubber back rest. Once that was done, the top box mounting plate was checked over before being fitted to the bike… … which required the luggage rack bolts to be eased off and the mounting plate slid into place up and under the top rail of the rack before being pulled back towards the rear of the bike and located. Which allowed the top box to be mounted… … finishing that box off and allowed me to move onto the panniers. After inspection a few issues were found, so I set about sorting those out. First of these was the opening strap on one was broken off, so a new one was fitted. I then moved onto the hinge, which had taken a little more wear than was normal, due to the strap being broken… … so these were replaced by driving the old hinges off and the new ones tapped into place with a copper-hide and a small block of wood, in a controlled manner so that nothing was damaged. While I was in there, a new bungee strap for this pannier was ordered and fitted as the old one was a bit shot. Next up were the ‘touring’ badges, which had seen better days, so the first had been eased out with a car trim removal tool and the recess scraped clean of adhesive, before the second was fitted… … which made much more of a difference to the look of both panniers than I expected. The only job remaining was the bump strip on the bottom of one of the panniers… … so this was removed and the mating face cleaned up and a new one ordered. Unfortunately the only one available was from Italy, took a while to arrive and cost a fair amount to import to the UK, but it’s got to be done! With the panniers back in one piece they were also given the sandpaper and very sparing linseed oil treatment… ... which bought them up really nicely, allowing these to be mounted to the bike and allowed the pannier liner bags to be fitted… ... finishing up that job, so it's just down to the check over and fixing any snagging issues. As always, if you'd like further details, please see https://motorcycleprojects.wordpress.com/ -
BMW K75RT Ultima Restoration
wollyjumperuk replied to wollyjumperuk's topic in Old Motorbikes, Projects and Restorations
Hey Ian, I would have done exactly the same as you, bar I would have given the mirrors a clean down with cellulose thinners before any paint then used a tac-cloth - saying that, the finish looks good! I would agree, don't touch them, don't be tempted to check if they are smooth for at least 24 hours (and keep any dust away from them, as it'll stick!). The paint will possibly be soft for up to a week, so best to leave them somewhere and forget about them until a week has passed. I find the finish is dependant mostly on the surface preparation, then how you sprayed the paint and how long you left between coats - I found Brad Angove (https://www.youtube.com/user/BradAngove) really useful on youtube. Chris -
BMW K75RT Ultima Restoration
wollyjumperuk replied to wollyjumperuk's topic in Old Motorbikes, Projects and Restorations
I just find it easier to go step by step, otherwise I would get confused! Get something as good as it's going to be before moving on. I had the gearbox apart as there was a bit of resistance to some gear changes, but that turned out to just be a much needed gearbox oil change! THe engine was good before I started, so that just had a going over and a service to check as much as I could without significant disassembly. I've pretty much put everything I did on this thread if you want to take a look, the additional bits with a few more photos and explanation are on my blog (linked below) I have been following the restoration but don't remember much or anything about engine/gearbox but I may have just forgot about it I've just had a look and your right, I completely failed to post about it, possibly because my hands were so covered in oil and grease handling the camera would have been tricky! I've done all this solo so some bits may have been missed due to this. To be honest, there wasn't much to say bar the engine had a check over and the gearbox had new oil (after the clutch pushrod seal was sorted). -
BMW K75RT Ultima Restoration
wollyjumperuk replied to wollyjumperuk's topic in Old Motorbikes, Projects and Restorations
I just find it easier to go step by step, otherwise I would get confused! Get something as good as it's going to be before moving on. I had the gearbox apart as there was a bit of resistance to some gear changes, but that turned out to just be a much needed gearbox oil change! THe engine was good before I started, so that just had a going over and a service to check as much as I could without significant disassembly. I've pretty much put everything I did on this thread if you want to take a look, the additional bits with a few more photos and explanation are on my blog (linked below) -
BMW K75RT Ultima Restoration
wollyjumperuk replied to wollyjumperuk's topic in Old Motorbikes, Projects and Restorations
I can't ever profess to this being better than new, I would settle with as good as I could make it - I am sure someone with more skill would have done better, but if I don't like the way something has turned out I tend to strip it back and start again, up to a point at least! -
BMW K75RT Ultima Restoration
wollyjumperuk replied to wollyjumperuk's topic in Old Motorbikes, Projects and Restorations
Not quite there yet, I've got some touch up bits I need to do (bits I'm not completely happy with that I've become mildly obsessed by really, when you live with a restoration for 2 years, there will always be a bit of paint you've managed to ding here and there!), a few finishing touches here and there (like the fairing infills and the black plastic bits, I need to figure out how they can look better), a very small oil leak from the oil pressure sensor (which looks to be a common fault, so I have a new one of them to go on), and of course the luggage that has so far been gathering dust and holding other bits awaiting addition to the bike. Once all that is done, then the MOT, tax and insurance so I can take her for a good ride - I hope that I get on with her and she isn't a disappointment after all the effort, but if I don't then I'll look to move her on probably at no more than she has cost me to do, so someone will get a solid bike without the cost of the labour (or the time) to do her up. -
BMW K75RT Ultima Restoration
wollyjumperuk replied to wollyjumperuk's topic in Old Motorbikes, Projects and Restorations
Onto the remaining decals and various stickers for the K75 to bring this back as close to original as I can. It's worth saying at this point that all surfaces were prepared with a good clean and a tac-clothing to remove any loose material before anything was even offered up, let alone stuck down. First up was the 'RT' badge, which had been eased off, which meant that although the foam backing was still present... ... an adhesive needed to be added. This was done by applying double sided tape, placed face up and covered with a cloth to protect it, before a paint tin was used to weigh it down overnight, to ensure the tape had stuck well before the tape was trimmed back... ... ready for application. Before the badge was removed the position of the top left of the R was measured as 1" up from the headlight surround and 2 1/4" in from the corner to the right of the headlight surround, so this position was marked very lightly, to allow the badge to be aligned and held in place... ... and once I was happy with how this looked, the badge was flipped up and the backing of the tape removed before this was carefully placed... ... finishing off the front end nicely! Next was onto the underwear stickers, starting with the missing sticker from the tail section cover which, despite cleaning, this up the location for the missing replacement part sticker, which allowed this to be directly placed by hand and the cover put back on the bike... ... so with the seat up, the stickers on the base of the tail section were laid out, this was played with for a while to get the alignment as close to square and the original pictures of this bike as I could. Once I was happy with alignment these were held in place with masking tape... ... before the backing was eased off, the sticker was laid into place and the air slowly pushed out... ... which finishes off the stickers on the tail fairing. With that done, the next stickers were for the ABS pumps and again I studied the original photos taken of the K75 to check alignment, and a bit of online research led me to a decision - red or silver ABS decals, they seem to be interchangeable, so I went with silver to tie-in with the bodywork. As with the other decals, it was popped into place and held with masking tape... ... to allow the backing to be peeled off and the decal stuck to the surface and any trapped air gently worked out, with the decal worked around the contours of the pump, before the front cover was gently pulled off... ... I found that pulling both front and back off, towards the unpeeled section of the sticker, effectively doubling it over on itself, was best at leaving the decal where it should be... ... and as that pump was done, the other followed in short order. With all of the different types of stickers and decals used here, the same was done for the homogenisation decal... ... followed by the unleaded fuel decal... That brings me onto the most important decal on the bike, the 'Ultima' logo, I took a lot of time in aligning this on the bike... ... before I was confident enough the remove the backing, stick it down and begin peeling the front off, leaving the logo as it should be and looking good... ... with the same done to the far side of the bike. As always, if you'd like further details, please see https://motorcycleprojects.wordpress.com/ -
BMW K75RT Ultima Restoration
wollyjumperuk replied to wollyjumperuk's topic in Old Motorbikes, Projects and Restorations
Hopefully not long, just a few decals to pop on, touch up a few bits, get the luggage up together, MOT and give it a run for a while. I did ride this for a bit before I stripped it down and it didn't really float my biking boat! But a few years ago I got talking to a guy in Honister Hause youth hostel who turned up on a K75RT before a few obligatory drinks were had, and he advised to take the bike for a long run over a few days (sounds like an excuse for a bit of a tour) before I draw any conclusions. But, I must admit if I don't get on with it on the second go I will offer it for sale. -
BMW K75RT Ultima Restoration
wollyjumperuk replied to wollyjumperuk's topic in Old Motorbikes, Projects and Restorations
Now I can't remember why, but I put the spark plug to one side when I was doing the engine, as I've found it again it's time to get it done! So, it was grabbed out... ... and the majority of the old, and in places bubbling, paint was taken off with a wire brush attachment on a drill, leaving just the bits the brush couldn't get to. These were treated with Rust-oleum NR.1 Green Paint Stripped, which lifted the remainder with 2 treatments, so this could be washed off and put in the sun... ... to dry off. Once dry, a polishing mop was popped on the drill and the BMW lettering was polished up, as this was the finish I wanted on these... ... with these covered with masking tape and this cut back just to cover the lettering with a scalpel (in the fiddly bits) and the old gasket making method (I'll let you look at my posts on the other engine covers for that one), so it was ready to paint... ... just as soon as I'd cleaned it down with white spirit and allowed it to dry. With that done, the piece was given a few coats of Halfords Engine Paint, the one that cures at room temperature, mainly for ease and to match the other engine covers. The masking tape was removed very carefully with a scalpel and a pair of needle nose pliers as soon as the last coat had gone on... ... so the tape didn't set into the fresh paint as it cured, I'd made that mistake before! Once that was cured, the cover was bolted onto the engine with a set of new stainless steel bolts... ... finishing off that little job! As always, if you'd like further details, please see https://motorcycleprojects.wordpress.com/ -
BMW K75RT Ultima Restoration
wollyjumperuk replied to wollyjumperuk's topic in Old Motorbikes, Projects and Restorations
I've held off doing this as I wasn't sure how I wanted this to look. From the factory these came in either polished chrome or black, and after some thought I decided to go for black. So, the heat shield was grabbed up... ... and new stainless bolts ordered to set this off. The heat shield was cleaned up with a wire brush attachment on a drill... ... both front and back to roughen the surface a little ready for the paint, before being cleaned down with white spirit and allowed to dry off. The heat shield was treated to a few coats of Halfords Engine Paint... ... before it was allowed to cure off. Once cured, the square nuts were slipped into the retainers and the new bolt threads given a light smear of nickel grease to reduce the risk of corrosion and the heat shield mounted... ... now, I think that looks fairly smart and completes the exhaust finally! As always, if you'd like further details, please see https://motorcycleprojects.wordpress.com/ -
BMW K75RT Ultima Restoration
wollyjumperuk replied to wollyjumperuk's topic in Old Motorbikes, Projects and Restorations
Time to go for the last piece of bodywork, with the side panels, so there were grabbed and put on the bench... ... these were a bit dinged in places, so they were rubbed down with 1000 grit wet and dry paper, ready for painting... ... these were then given a sacrificial coat of primer to highlight the smaller dings, which allowed all the defects to be filled and rubbed back before coats of Autotek Etch Primer, Halfords Arctic Silver and Halfords Petrol Resistant Lacquer, following the directions on the can and rubbing down in between coats... ... and left to cure for a week. Once cured, the rubber stops were added to the mounting pin and the tank mounts, before each of the side panels were put into place... ... thankfully finishing off the body work painting. As always, if you'd like further details, please see https://motorcycleprojects.wordpress.com/ -
BMW K75RT Ultima Restoration
wollyjumperuk replied to wollyjumperuk's topic in Old Motorbikes, Projects and Restorations
With the mirrors sorted, it was time to neaten up the front end with the fairing infills. So, first up were the mounting brackets, which were checked over before being cleaned down with trusty WD-40 on a rag and with nothing else needed here (except me needing to buy shares in the WD-40 company), these were bolted into the front fairing... ... so the focus could switch to the infills themselves. All the infill panels were arranged on the bench and, except a bit of dust, everything looked good enough to use, so thankfully no waiting around for spares on this one! I grabbed the lower panels first and found that one of the units was missing the foam/rubber strip... ... and the other was in such a condition that daylight could be seen through it, so much for no spare parts! Thankfully I had some black rubber tubing that was perfect for the job. This was cut to size and sliced down it's length, allowing this to be super glued into place, once the old adhesive had been removed... ... finishing the required repair work to that piece. The lower infill panels were both given the WD-40 treatment, and the lower mounting point for the infills were given a new stainless clip, allowing the lower fairing infill panel to be fitted with a new stainless steel bolt... ... on each side, the bike is already looking much better with these in place. Next up was the forward dash / infill panel, which was a bit dusty, but otherwise in fairly good shape. The dash light fitting was hooked up to a spare bike battery to make sure everything worked... ... with no issues found the infill was cleaned down, this time just with water and a clean paintbrush to get rid of the lose material. Once dried, the blank switches were popped back into the unit, which was offered up to the bike to allow for electrical connections to be reinstated before the windscreen unit was loosened off so the infill could be slid into place and electrically tested... ... to confirm everything was fine, allowing the panel to be fitted into place. Finally the pockets and the lids were up, I've worked on this previously when I got the bike, one of the lids was bubbled, like it had been exposed to a flame or something very hot, I grabbed a replacement while I was looking for other bits on the bike. The parts were cleaned up with water and a paintbrush and allowed to dry. Once they were dry each of the pockets were fitted in turn... ... once in, the seals were checked on the lids to make sure that they would keep water out of the pockets and they looked good, so these were fitted and the locks checked they worked with the ignition key. Standing back, this looks pretty good to me... ... finishing this off and bringing the bike closer to completion. As always, if you'd like further details, please see https://motorcycleprojects.wordpress.com/ -
BMW K75RT Ultima Restoration
wollyjumperuk replied to wollyjumperuk's topic in Old Motorbikes, Projects and Restorations
With the front fairing done, windscreen in place and the fairing infill about to go in, this is the best time for me to tackle the mirrors. I've taken into account a common issue seen with these, if they smack something they fall off and generally end up under the vehicle which just knocked them off for you - tethering is the way to combat this problem according to many. With that in mind, the mirrors were popped on the bench so that work could begin... ... and the only work needed was to the housings themselves, having been dinged a bit over time. To get this done, the glass had to come out, so the corners around the mirror glass were masked up to limit damage... ... and tape put across the glass, just in case I break it! And to save my eyes, in case I shatter it, alongside the safety glasses... ... so all was safe to proceed. This is convex glass (trust me, that bit is important to see what's going on behind you), it can be a bit expensive to replace, so from here on in I am going very carefully. A car trim removal tool was slid behind the mirror glass and put as close to the ball connector possible before gently easing the mirror glass and holder out... ... thankfully both in one piece! On inspection of one of the mirrors, the housing didn't quite close properly, and there as a scrunching noise as I tried to press it back to place, so easing around the join with the car trim tool I eased the housing away. I found something odd, expanding builders foam... ... I suspect this had been used to 'glue' the mirror back together after an impact at some point in history. It's not meant to be there, so I got as much of it out as possible, thankfully this does not seem to have done too much damage to the function of the housing. While this was open, an 8mm hole was drilled below the mirror glass mounting point so the tether could be pulled through... ... with a further 8mm hole drilled into the plate between the 2 lower mounting points to allow the tether to be fed through to the bodywork. With the tether fitted, the mirror glass mount was reinstated and the tether looped over it and the hole between the 2 mounting points was measured and a corresponding hole drilled through the front fairing, so that the tether can be passed through. The mirror mounts were loosely bolted into the front fairing, ensuring the rubber washer is between the mount and the fairing... ... to allow the mount to sit away from the fairing and the tether enough space to emerge and be looped around the mount. As a demonstration I held the mirror up to the fairing to see where this would hang... ... which seemed to work OK enough, so carry on I did. With that done, the mirror housing was glued back together, nothing special here, just a bead of super glue run around the mating faces, before it was held together with masking tape while it cured off. Once cured, the body of the mirror housing was looked at and the larger areas of damage filled with body filler ready for the sanding to commence! The sanding took both mirror housings back to a smooth finish with the vast majority of the imperfections removed and the remained of the paint finished scuffed to accept the new paint, which meant it was ready for the sacrificial coat of etch primer, to identify any further dings I'd missed, which were then sanded back again and the painting proper to start with Autotek Etch Primer... ... once that was on and cured they were rubbed back with 1000 grit wet & dry paper, drying off once a smooth finish was achieved. The housings were allowed to dry off before coats of Halfords BMW Arctic Silver were applied... ... followed by a further run back, dry and coats of Halfords Petrol Resistant Lacquer and again allowed to cure off. Once cured and masking removed, the foam mounting pads were installed with a little spray contact adhesive, making sure they were correctly aligned first time! Next was the mirror glass, each of which had the ball socket lightly greased to aid fitting and adjustability once fitted. In turn, each was held in place and a steady pressure against the center of the mirror used to pop it back into place and the tape removed from the glass... ... leaving each of the mirrors ready to be installed. To install the mirrors the tether was fed through the pre-drilled hole in the fairing and looped around the rear most mounting plate bolt (behind the washer), while the mirrors were snapped onto the retaining lugs... ... which was a right pain, so the top mounting was done first, then the bottom 2. With the those fitted, that was job done on the mirrors! As always, if you'd like further details, please see https://motorcycleprojects.wordpress.com/ -
BMW K75RT Ultima Restoration
wollyjumperuk replied to wollyjumperuk's topic in Old Motorbikes, Projects and Restorations
Before I got into the fairing infill panels, and because I originally wanted to mount these gauges in the infill panels, I wanted to get these gauges done. The mounts and gauges were popped on the bench... ... so I could check condition, starting with the mounts. These were found to be fairly corroded, under the paint, causing a bubbling of the paint surface... ... which was taken back with an angle grinder with a sanding disc, to try and minimise damage to the metal beneath, so that the pieces could be rubbed back with 1000 grit wet and dry sandpaper and hung ready for painting and tac-clothed to remove the loose material. With that done, the mounts had coats of Autotek Etch Primer... ... and once cured, coats of Halfords Gloss Black... ... and finished of with coats of Autotek Petrol Resistant Clear Lacquer. With these having a few days to cure off, they were ready to fit to the handlebars, which meant removing everything from each side and sliding the mounts into place... ... remembering to check which side they go on first before securing with stainless steel bolt and washers. With the brackets fitted, each of the gauges were cleaned up, with the trusty WD-40 rag... ... with the only things left to do is to mount and test them. The gauges were bolted into position... ... and electrically connected, with the position adjusted for now and the nuts nipped up. To functionally test the fuel gauge, as previous tests had shown the sender to be good, the ignition was popped on and a length of wire used to hook the float in the fuel tank up off the stop... ... and secured by popping the end down the overflow hole. With that secured the gauge was checked, which read as expected and then moved when the float was raised and lowered. The temperature gauge was tested by running the bike until the needle started to move, showing that was all operational. As always, if you'd like further details, please see https://motorcycleprojects.wordpress.com/ -
BMW K75RT Ultima Restoration
wollyjumperuk replied to wollyjumperuk's topic in Old Motorbikes, Projects and Restorations
With the front fairing on, it was time to get the next biggest piece out of the way, partly as it get fits directly onto the fairing and partly because I don't want to move it to get to other parts anymore! So, again as usual, all the components were laid out on the bench... ... and I firstly concentrated on the base, which looked in good condition and as this worked well no intervention was needed, so the mechanism was removed from the mounting plate, allowing this to be cleaned up. Of course, this was done with a rag and WD-40. Because when you can't cleanse with fire only WD-40 will do! So the underside was cleaned, followed by the top side... ... once I was happy with that the mechanism was reattached and the components here-in were concentrated on, including removing the return springs, so these can be inspected, cleaned (again with WD-40 on a rag - I've got a good collection of WD-40 soaked rags now!) and reattached to it's mounting points with a spring puller, for ease, and the remainder of the mechanism was cleaned up... ... allowing the springs and slide shafts to be greased up accordingly, to save wear or stiffness in future. With that done, the assembly was put into place on the front fairing to ensure fit... ... and all looked good, once I managed to slide the motor into the hole behind the headlight and as I was happy with that, the unit was plugged into the wiring loom and the operation of the mechanism tested to ensure it works and all was found to be good. With that, the assembly was removed and new stainless steel fairing clips were put onto the front fairing... ... so this is ready for the final mounting of the unit. With that done I was able to concentrate on the bumps and scrapes on the mounting plate, I waited until this point to sort these out, just in case I caused any more with the first fitting... ... these were further cleaned up to remove any WD-40 residue, a little gloss black spray paint sprayed into the cap and a brush used to touch these in... ... blending in the damage to make it less noticable. I didn't want to try and fill these as the sanding process would damage the mounting plate more. With that done, the windscreen drive and mounting unit were bolted into place with brand new stainless bolts, to match the others on the bike... ... so hopefully I will not have to remove it again! With that done, it was onto the windscreen itself and first look at the screen showed a few bubbles behind the cleaning instructions... ... these were pricked with a sharp (I got a new blade out especially) scalpel blade, a needle would have been just as good, to allow the trapped air to be massaged out via the hole... ... which looks good and gets rid of the air trapped in the BMW factory in 1995/6. The mounts for the screen were popped off... ... and showed the scale of cleaning needed on the windscreen! Without waiting around I cracked on with 2 hours of gentle cleaning, following the instructions on the screen, soaking and cleaning small sections of the screen at a time, drying before I move onto the next section and ensuring these sections overlap... ... leaving the screen nice and clean afterwards. The screen mounts were inspected and found to be solid, so we're cleaned up with a wipe of WD-40 on a rag, ready to be fitted back into place. The forward rubber mount was installed first, before the plastic fixings were added before the rearward rubber mount was laid into place and this was pushed (well more gently coaxed) into the groove with the flat side of a small screwdriver... ... aided by a smear of WD-40 to help it slide into place. This then allowed the screen to be mounted... ... and functionality tested again, with just the drain lines to fit to finish the job. These were gathered together, inspected and found everything was good to go, so the clips were added to the front fairing lower panel... ... this was followed by the lines threaded behind the headlight and connected to the drain points on the windscreen mounting... ... and the other end passed into the clips, making sure these face to the rear of the bike to ensure drainage when the air pressure is on the front of the bike while riding. That's the windscreen done! As always, if you'd like further details, please see https://motorcycleprojects.wordpress.com/ -
BMW K75RT Ultima Restoration
wollyjumperuk replied to wollyjumperuk's topic in Old Motorbikes, Projects and Restorations
Now, I've not been looking forward to this giant lump of fairing, but here we go! To start, the RT badge was heated with a hair dryer so this could be easily eased off, leaving me with the bare fairing which was rubbed down with 1000 grit wet and dry sandpaper to prepare it for painting... ... and thoroughly cleaned with clean water, hand dried and allowed to further air dry for a few hours before filler was applied to the imperfections and allowed to set overnight. From there, with a fair amount of effort, a sunny morning and more 1000 grit wet and dry sandpaper, the fairing was properly rubbed down... ... followed by another wash and dry. Once dry the fairing was cleaned with a Tac-Cloth and then white spirit, allowed to completely dry before a couple of coats of Halfords Etch Primer and allowed to cure overnight before flattening off with 2000 grit paper, cleaned, dried and finally 3 coats of top coat... ... and allowed to cure overnight.The preparation work was completed again before 3 coats of Autotek Clear Lacquer and allowed to cure for the final time. Meanwhile the bottom section of the fairing was inspected and found to be defect free, so was cleaned up with WD-40 on a rag... ... and allowed to dry off while the fixings were replaced with stainless steel alternatives. With the fairing cured, the indicators were slotted in and bolted... ... before the rubber seal was fitted into headlight and the unit was bolted into the fairing... ... checked for fit and, thankfully, all good! The mounting points were given new fairing clips before fitting the infill panel to the underside of the fairing... ... ready for test fitting. The fairing was slotted onto the bike and secured with the 4 fixings surrounding the headlight, to allow all of the alignment to be checked... ... which all looked good, bar 2 fixings, unfortunately the 2 most difficult to alter - the 2 frame mounts, hidden behind the lower fairings... ... and all looked good, so everything was rebuilt, including the internal infill panel, leaving the front fairing fitted! From there was the wiring connections, because I had labelled all of these when I was disassembling the bike, this was just a case of reading - removing the label - plugging in. Once completed, each of the electrical components were tested in turn, starting with indicators... ... then the sidelight and headlight (both main and dipped beam)... ... finishing off the electrical installation, so job done! You can't believe how much I'm glad that's over, I'm definitely not a fan of painting, but it's got to be done! As always, if you'd like further details, please see https://motorcycleprojects.wordpress.com/